In Belement lab, we conduct salt fog/salt spray testing to simulate corrosive environmental conditions and evaluate the durability and performance of materials, coatings, and components when exposed to salt environments.
Capabilities Available in the Laboratory 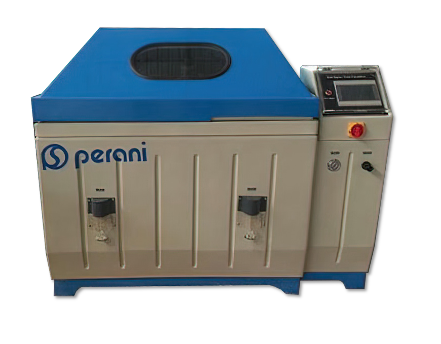
Model YWX-250BP Chamber
- Operational Volume: 300 liters
- Construction Material: Fiberglass
- Temperature Range: +5K to +55K
- Thermal Deviation: ±0.5K
- Humidity Range: Up to 85%
- Spray Density: 0.5–3 ml/80 cm² per hour
1. Purpose of Fog/Salt Testing
- Corrosion Resistance Evaluation: Test how materials and coatings respond to prolonged exposure to salt environments.
- Coating Quality Testing: Validate the effectiveness of anti-corrosion coatings such as zinc, chrome, or protective paints.
- Marine Environment Simulation: Simulate humidity and salinity conditions similar to coastal, marine, or salt-treated road environments.
- Product Life Assessment: Determine the durability of products over time under harsh environmental conditions.
2. How Salt Fog Testing is Performed in the Lab
- Controlled Testing Chamber: Samples are placed inside a dedicated chamber that generates a salt fog containing a fixed concentration of salt solution (typically 5% sodium chloride NaCl).
- Testing Conditions:
- Temperature: Approximately 35°C (as per standards).
- High Humidity: The environment is saturated with salt fog.
- Duration of Exposure: Varies depending on test requirements (from a few hours to hundreds of hours).
- Monitoring: We monitor:
- Corrosion progression on the samples
- Physical changes such as rust formation, bubbling, or coating delamination
3. Applications of Salt Fog Testing
-
- Automotive Industry:
- Testing durability of car parts (e.g., metals and coatings) under exposure to salt.
- Electronics Industry:
- Evaluating corrosion resistance of connectors, printed circuit boards (PCBs), and metal components.
- Construction and Coatings:
- Verifying the quality of anti-corrosion paints and metal coatings (e.g., galvanizing).
- Marine Industry:
- Assessing materials used in marine environments exposed to saltwater and humidity.
- Consumer Products:
- Evaluating the durability of household or industrial products in humid, salty environments.
- Automotive Industry:
4. Testing Process
-
- Sample Preparation:
- Cleaning and preparation of the sample according to test standards.
- Test Execution:
- Placing samples inside the chamber and generating salt fog at controlled concentration and temperature.
- Testing is performed for a predefined duration based on test requirements (e.g., ASTM B117 or ISO 9227 standards).
- Monitoring During Testing:
- Tracking corrosion progression and its effects on the sample surface.
- Post-Test Analysis:
- Inspecting samples for:
- Rust formation or discoloration
- Coating defects such as bubbling, cracking, or delamination
- Comparing findings against standard requirements or product specifications.
- Inspecting samples for:
- Sample Preparation:
5. Benefits of the Test
- Accurate Simulation of Corrosive Environments
- Quality Evaluation of Coatings and Metallic Structures
- Early Detection of Potential Product Failures
- Improved Product Quality and Reliability in Harsh Conditions
6. Common Standards Used in Salt Fog Testing
- ASTM B117: The most widely used standard for corrosion testing in salt fog environments.
- ISO 9227: The international standard for corrosion testing.
- JIS Z 2371: The Japanese standard for salt fog corrosion testing.
Conclusion
Salt fog testing in our lab provides accurate and reliable assessments of product durability under high-salinity conditions. Whether testing components for the automotive industry, anti-corrosion coatings, or marine-use materials, we ensure high-quality, reliable results that help improve product resilience and longevity.
For more information or to schedule testing, feel free to contact us!