In our lab, we conduct altitude testing to simulate high-altitude conditions and evaluate the performance, safety, and reliability of products and materials when exposed to low-pressure environments. This is essential for industries where products operate in environments with varying atmospheric pressures.
Capabilities Available in the Laboratory 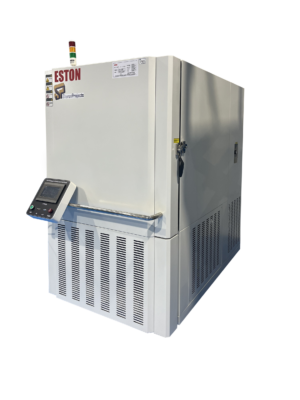
Model 408DQY Chamber
- Operational Volume: 408 liters
- Temperature Range: -75°C to +150°C
- Thermal Deviation: ±0.5K
- Heating Temperature Change Rate: 3.5K/min
- Cooling Temperature Change Rate: 1.2K/min
- Pressure Range: 86~106 kPa
- Low Pressure (Altitude) Testing: Complies with MIL-STD-810G METHOD 500.5
1. Purpose of Altitude Testing
Altitude testing serves the following goals:
-
- Aerospace and Aviation: Validate equipment performance at high altitudes where atmospheric pressure and oxygen levels are low.
- Automotive: Assess vehicle components that operate in mountainous or high-altitude regions.
- Electronics: Identify failures such as arc flash, overheating, or malfunctions caused by low pressure.
- Packaging and Seals: Test the integrity of sealed packages, ensuring no leaks under reduced pressure.
2. How Altitude Testing Works
-
- Pressure Simulation: The chamber reduces pressure to simulate altitudes ranging from sea level up to 30,000 feet (or higher).
- Environmental Conditions: In addition to altitude, we can simulate:
- Temperature variations (hot or cold)
- Humidity levels
- Combined thermal and pressure cycling
- Monitoring: Using precise sensors, we monitor:
- Chamber pressure
- Temperature
- Component behavior (mechanical and electrical performance)
3. Applications of Altitude Testing
- Aircraft Systems and Components:
-
- Assess avionics, cabin equipment, and fuel systems under low-pressure conditions.
- Electronics and Batteries:
-
- Validate the functionality of devices such as sensors, PCBs, and batteries that may fail at high altitudes.
- Detect potential issues like outgassing, electrical arcing, or voltage breakdown.
- Medical Devices:
-
- Test devices like oxygen regulators, ventilators, or sealed components for high-altitude operations.
- Automotive Parts:
-
- Evaluate engine performance, fuel systems, and tires in reduced-pressure environments.
- Packaging Integrity:
-
- Ensure no leaks or structural failures in sealed packaging, especially for pharmaceuticals or food products.
4. Testing Process in Our Lab
- Setup:
-
- Place the test sample inside the altitude chamber.
- Configure sensors to monitor environmental and sample conditions.
- Simulation:
-
- Gradually decrease pressure to simulate the target altitude.
- Combine temperature and humidity profiles as required.
- Monitoring:
-
- Observe real-time data on pressure, temperature, and sample performance.
- Post-Test Analysis:
-
- Inspect for physical changes such as leaks, cracks, or material failures.
- Verify functional performance under simulated conditions.
5. Challenges to Watch For
-
- Outgassing: Materials may release gases under low-pressure conditions, which can impact performance.
- Electrical Issues: Low pressure can cause electrical arcing in components.
- Seal Integrity: Sudden pressure changes may compromise seals or packaging.
6. Outcomes and Benefits
-
- Ensure products meet performance standards at high altitudes.
- Identify weaknesses early in the design phase.
- Improve reliability for aviation, automotive, and electronics applications.
- Ensure compliance with industry regulations and standards.
Our altitude testing capabilities allow us to simulate real-world high-altitude conditions to validate product performance and reliability. If you need further details or wish to schedule a test, feel free to reach out!